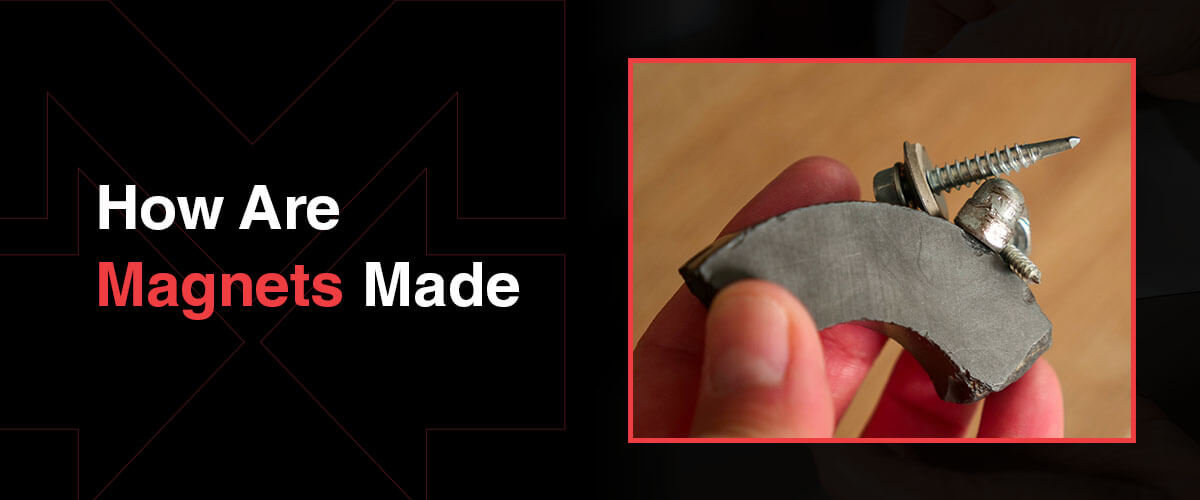
How Are Magnets Made?
Magnets appear in motors, headphones, loudspeakers, toys, machinery, and more. Magnets power the modern world, but few people understand what they are or how they work. Discover the magnet manufacturing process and the different types of magnets we use.
What Are Magnets?
Magnets have magnetic fields that can repel or attract other objects. While some materials are naturally magnetic, others can become magnetized or demagnetized under some conditions. Similar to an electric current, magnetism is the result of electrons moving.
As the electrons spin, they create a dipole with a north and south pole, with one end being the opposite of the other. This action is what causes repulsion and attraction to other objects. Placing two north-pole or two south-pole ends of magnets together will result in repulsion, and the objects will not connect. However, a south pole will attract a north pole to bring the objects together.
There are three categories of magnets:
- Permanent: An excellent example of a permanent magnet is a refrigerator magnet to hang notes on the door. These magnets emit a magnetic field without needing electrical power or an external magnetism source. There are “hard” and “soft” permanent magnets. Soft magnetic fields can lose their magnetism quickly when used in magnetic shielding objects, such as transformers.
- Temporary: These magnets act like permanent magnets only when a magnetic field is present. Temporary magnets lose their magnetism when you move them away from objects with magnetic fields. Annealed iron and steel are examples of temporary magnets. An everyday temporary magnet example is when paper clips stick together when a permanent magnet is nearby.
- Electromagnets: Electromagnets need an electricity source to behave like a magnet. The electric current passing through the object generates the magnetic fields. These magnets appear in various applications, such as headphones, generators, and motors. Although these magnets can be very powerful, you can turn the magnetic force on and off with the push of a button.
What Are Magnets Made of?
Magnets are made of ferromagnetic metals, such as iron, cobalt, and nickel. These metals can magnetize uniformly. Manufacturers rely on five materials to create permanent magnets:
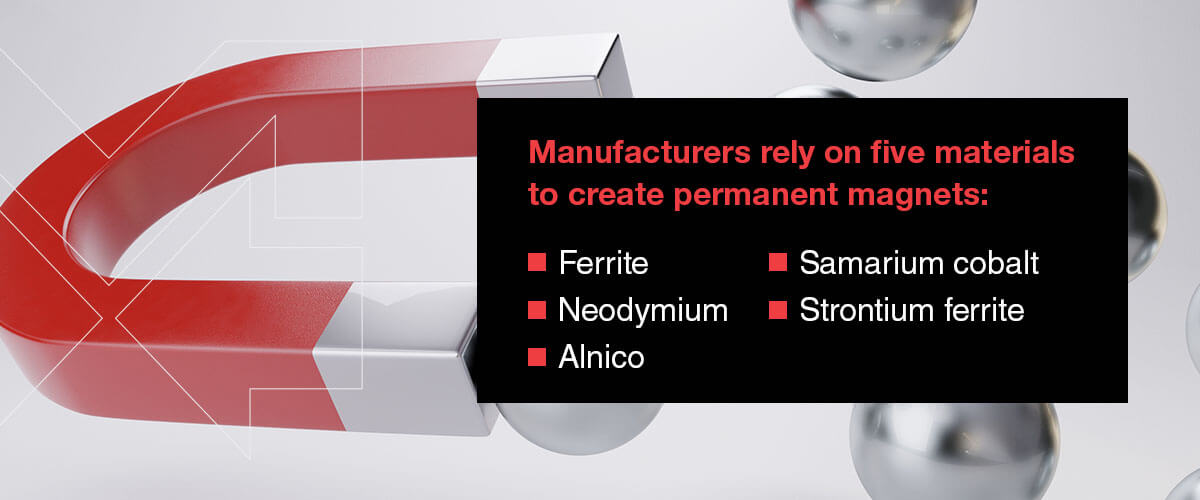
- Ferrite: This term refers to pure iron or an iron oxide and strontium carbonate or barium compound. Ferrite magnets are weaker than other types but have low production costs.
- Neodymium: This rare earth element mixes with boron, iron, and traces of other elements to create a magnetic alloy. Neodymium magnets are most common for industrial and commercial applications due to their superior strength.
- Alnico: This term refers to a combination of cobalt, nickel, and aluminum. Alnico magnets are also very strong and often appear in loudspeakers, generators, and motors.
- Samarium cobalt: This rare earth alloy often contains traces of zirconium, hafnium, copper, iron, and praseodymium. Samarium-cobalt magnets are often used in extreme conditions, such as high temperatures or corrosive environments.
- Strontium Ferrite: Combining a strontium ferrite powder with a rubber polymer creates flexible magnets. Flexible rubber magnets are often found in strips and have high resistance to the natural elements, making them suitable for outdoor and indoor applications.
However, some magnets are natural rather than humanmade. For example, lodestone attracts iron, making it a natural magnet.
The Magnet Manufacturing Process
Several processes can create magnets, but powder metallurgy is the most common. Samarium-cobalt, ferrite, and neodymium magnets are made using this method.
The process begins by melting suitable raw materials in an induction melting furnace. After melting, the alloy goes into a mold, processes in a strip caster, or rests on a chill plate. After this step, manufacturers compact the powder, which involves aligning the particles so all magnetic regions point in the same direction. This can be done through:
- Transverse or axial pressing: This process involves placing the powder into a tool cavity on the press. Before compaction, manufacturers apply an aligning field. Then, punches compress the powder into the tool cavity, which fixes this alignment in place. The aligning field is parallel to the compaction direction in axial pressing. During transverse pressing, the compaction is perpendicular to the field.
- Isostatic pressing: During this process, manufacturers fill a flexible container with powder, seal the container and apply the aligning field. After this, they place the container into an isostatic press, which applies pressure to the outside of the container using water or hydraulic fluid. This process compacts it equally on all sides.
After pressing, the materials go into a vacuum sintering furnace. The temperatures and use of vacuum or inert gas vary depending on the grade and type of magnet being produced. The magnet shrinks during this process and has a rough surface with no external magnetic field.
Finishing
Once the magnets obtain their rough shape, manufacturers move to the finishing step, which involves smoothing the magnet or slicing it into smaller pieces. They perform each of these processes very carefully to minimize cracking and chipping, as the magnet is very brittle at this stage. Additionally, magnet size, complexity, shape, and order quantity affect the manufacturing process most suitable for specific applications.
Manufacturers can create unique shapes with these magnets, but the alloys function best in simple forms. Manufacturers may use a vibratory bone to reduce sharpness before coating the magnets. Some magnets, like neodymium, need coatings as they are prone to react chemically or rust. Protective coatings often include epoxy, aluminum IVD, and electrolytic nickel, but conversion coatings like iron, zinc, or manganese phosphates and chromates can add temporary protection.
Magnetizing, Stabilizing, and Calibrating
After manufacturing the magnet, manufacturers need to charge it to produce the magnetic field. They accomplish this with a solenoid of fixtures imparting magnetic patterns. After charging the magnet, manufacturers may need to stabilize or calibrate it. Stabilization is the magnet’s pre-treatment, and calibration narrows the performance output range of magnet groups.
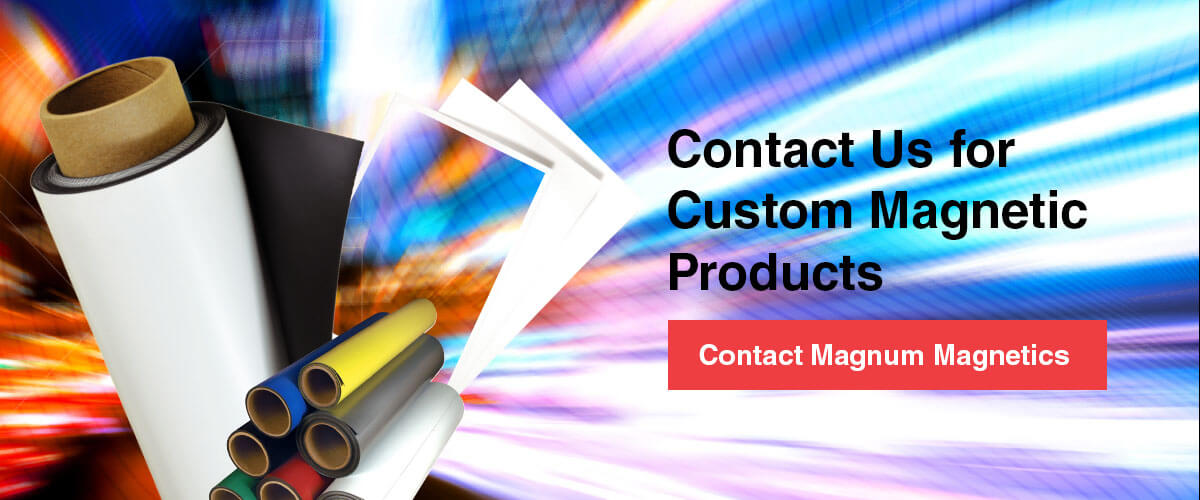
Contact Us for Custom Magnetic Products
Magnum Magnetics has been operating for over 30 years, and we continue providing superior customer service and competitive pricing for high-quality flexible magnet strips, sheets, and custom profiles.
We’re invested in maximizing our productivity through efficient equipment and employee training so we can reduce costs for our products. Our magnets are suitable for various applications across multiple industries, including advertising, retail, graphics, signs, engineering, and OEM applications.
Our flexible magnets use safe, quality materials, and we test each of our permanent magnets to ensure compliance with safety standards. Our competitive prices make it easy to find magnets at an affordable price while feeling confident in their quality.
Whether you need large advertisement signs, sheet magnets, magnetic strips, magnetic photo paper, magnetic buttons, or magnetic cards, we’ve got you covered. We’ll provide clear communication and help solve any challenges you face. Contact Magnum Magnetics to meet your magnetic needs.